top of page
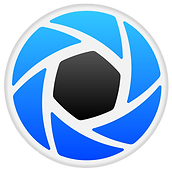
Keyshot Rendering/Animation
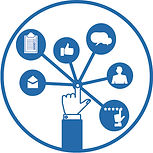
End to End Project Management

BOM & Part Costings
Skills in this Project:

Solidworks
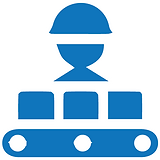
Plastic Injection Moulding

Photoshop/Illustrator
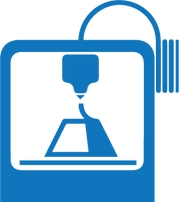
Rapid Prototyping

Electronic Enclosure Design

Optimising For Manufacture & Assembly
The Overall Project:
This was a project that I led at Evolve Group, where our client came to us with a previous design that needed to be optimised for injection moulding in Australia. The aim for the client was to have the parts ready to be tooled, reduce part costs, and improve the ease of assembly. While also be durable enough to withstand blasts in mines.

What is it?
The BMM is an impressive product that is placed in blast zones in mines all over the world. Once the blast occurs, the BMM will be shot with the material. This allows the crew to easily track where the material has landed saving time and money for the mines. The BMM consists of two products, the outer shell and the inner shell which I played apart in the redesign of both.
The Logo Addition:
Once the logo of use was approved, I went to CAD model it in areas that could be added via slides in the tool. Slides were used as they can create a logo that is an accurate representation of renders. Compared to an open-shut tool would have varying drafts on the feature making it almost non-recognisable. A slide is also good because it can be changed and modified if the client changes the logo in future.

The Final Prototypes:
From the client signing off on the technical drawings, we proceeded with a 1:1 professional prototype that offers near identical material surface finishes, tolerances and materials to a production model. This was done by an external supplier via the process of CNC for the plastic parts.
The Technical Drawings:
Below is a sample of the technical drawings provided to the client to sign off the design to proceed with the final prototype. Once the prototype is signed off, we would proceed to quote for tool manufacturing.
What I Learnt:
This project challenged me to learn more about injection moulding procedures while also being able to take an already-designed product to be optimised for plastic production. I learned more about material selection and moulding procedures to what would be cost-effective on a budget. I also learnt more about project management from end to end by communicating with the client and external stakeholders simultaneously. I also learnt more about electronic enclosure design in the types of ways to utilise ribs to secure parts in place. At the time of writing, this project is being tooled in China with T1 samples due in the next few months.

The Logo Positioning:
The client wanted the logo to be as large as possible on the part so it can be recognisable to the general public when promoting the product. I decided to have the logo on the slanted show faces as there is a large surface area to use.
Embossing was also used as de-bossing wouldn't look as clean as the material would shrink and close up the gaps.
Upper Part Horns:
This feature was added to prevent the inner shell from moving during a blast. The horns would crush when the outer shell is assembled preventing it from moving.
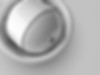


Venting and Snaps:
The upper part would attach to the lower part via 2 snap hooks. The snap hooks being aggressive would hold the parts in place and give the user feedback when assembled correctly.
Venting holes were also added along with a central hole as the client will fill the internals with epoxy.
Assembly Process:
Outer Shell Adjustments:
The client wanted to create a new tool with their new logo on the part, as the old tool needed too many repairs. The changes required were:
1. Remodel the design based on a 3D scan
2. Apply the new logo on the show faces, and be approved by the client
3. Add a ramp feature to the lower legs of the upper shell to improve the ease of assembly
4. Create a new assembly jig for staff to assemble onsite.

Exploded View:
This view shows the parts that would need to fit within this enclosure.
Inner Shell Adjustments:
After the outer shell was completed, our client wanted me to look into their new version of the inner shell. The inner shell is what would house the internal electronics that allow the product to be tracked via the mines. The client gave me a concept along with the electronics that would be required to be housed. The changes required were:
1. Remodel the design based on a provided concept
2. Ensure electronics fit and are secured once installed
3. Ensure the inner shell doesn't move around the internals of the outer shell during a blast
4. Decrease the cost of the current inner shell product that is being used
5. Improve ease of assembly
Internal Ribbing:
Both the upper and lower parts included ribbing, not only to add strength to the part but also to secure internal electronics in place. Sheer fits and guide ribs were used in the process to secure the parts together.

bottom of page