top of page
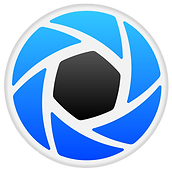
Keyshot Rendering/Animation
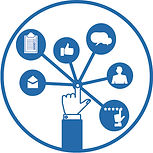
End to End Project Management

BOM, Part, Freight Optimisation & Costings
Skills in this Project:

Solidworks
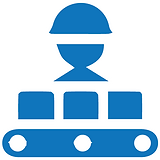
Plastic Injection Moulding

Photoshop/Illustrator
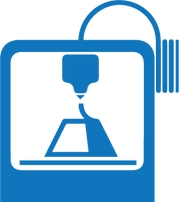
Rapid Prototyping

DFM & DFA Optimisation
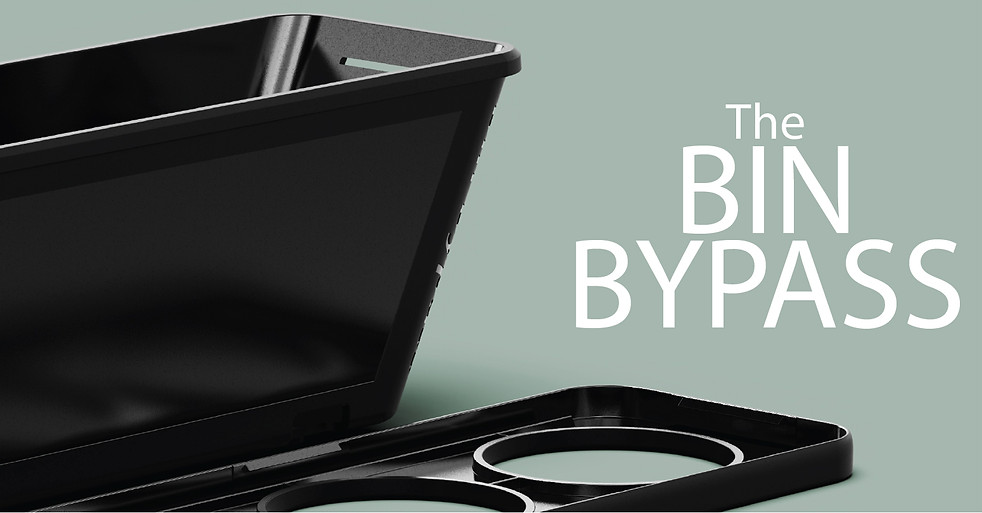
Optimising For Manufacture & Assembly
The Overall Project:
This was a project that I led at Evolve Group, where our client came to us with a previous design that was constructed out of metal that needed to be optimised for injection moulding in Australia. The aim for the client was to have the parts ready to be tooled, reduce part costs, improve ease of assembly, and optimise material selection and design features for the context of use.
Please see link to BinBypass website to hear about Kris & Jonathans story and vision: https://www.binbypass.com/
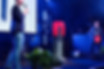
What is it?
The Bin Bypass is a 10c bottle/can refund station where the general public can deposit unwanted cans/bottles for someone else to take and claim. This product aims to reduce the amount of bin diving and littering that currently occurring in Australia. This compact product can be installed almost anywhere including poles, small/large bins, walls etc. This product is being rolled out in connection with Containers for change which a developing a large capacity station.
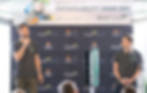
The Design:
The Bin Bypass was designed to be optimised for injection moulding, requiring minimal slides to reduce costs. A 2 part design was chosen due to ease of assembly during installation, where the front piece would snap onto the base via aggressive snap hooks. Making it difficult to remove.
The material used is a locally sourced HDPE/PP blend resin that can be durable as well as withstand UV.

The Prototypes:
During the design process, many 3D-printed prototypes were completed in order to perfect the snap fits, internal ribbing and how the cans/bottles would perform when deposited. This was crucial in creating a successful solution for the client before proceeding into tool manufacture. One 1:1 prototype was completed by an external supplier via CNC but unfortunately didn't get any photos at the time.
The Technical Drawings:
Below is a sample of the technical drawings provided to the client to sign off the design to proceed with the final prototype. Once the prototype is signed off, we would proceed to quote for tool manufacturing.
What I Learnt:
This was one of the first projects that I worked on at Evolve Group and it was a very eye-opening experience in designing products for plastic injection moulding. I learned a lot about the features of Solidworks and how to CAD models effectively for injection moulding. With regards to rib, snap hook, and material shrinkage specifications. I also learnt about pallet optimisation in creating a product that can be effectively packed onto pallets through carton stacking. At the time of writing, this project was heading into product manufacture through injection moulding at the start of 2024, with the tool arriving in Australia December 2023. In 2023 this design achieved a design award at the National Sustainable Building Awards.

Bottle/Can Assembly:
Internal ribbing was utilised to allow for the any cans/bottles to be stacked at an equal angle but also not allow for them to fall into the product. These ribs also allow for optimal pallet stacking, which would allow the client to fit more products onto a standard pallet.
Branding & Drainage:
Branding locations were in a different surface finish to allow installers to know the position to place the labels. Slides in the tool were also used to form the curved branding.
Slots at the top and bottom od the product allow for water or liquids to drain through the product instead of building up and adding additional weight.



Rear Mounting:
The client aimed to have this product installed in numerous locations. Keyholes were utilised at the rear allowing the product to be installed on either poles or bins. Side slots were also added so the client can add banding when attaching to poles.
A live hinge flap was added to the rear so rubbish or glass can be removed from the product if it builds up.
Other Images of the BinBypass:
What Needed to be Changed:
Upon the first review, the Bin Bypass required changes to be DFM & DFA optimised. The changes are:
1. Optimise for plastic injection moulding
2. Create a durable product that utilises sustainable recycled materials
2. Ease to install on poles, bins etc
3. Cans/bottles stack at the same angle and are easy to deposit and remove
4. Product cannot be easy to tear down; once installed, it needs to stay
5. Water and waste can cycle through the product. Glass or rubbish can be removed.
The 1:1Prototype:
When the detail design was finalised the client moved onto a 1:1 scale prototype made out of a black Polypropylene which represent similar to what the product would be inaction moulded from. This prototype is crucial for user/client testing as it is one of the last chances for finding any errors and flaws int eh design before moving to tool manufacture. As it would be costly and timely to make tool modifications to fix any design errors. I am proud to how this prototype turned out in how well the scan stack and stay in the product and the ease of mounting to public bins.
bottom of page