top of page

Solidworks
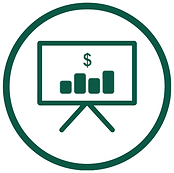
Business Model
Thinking

Photoshop/Illustrator

Sustainability Design
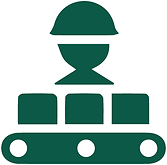
Design For Manufacturing
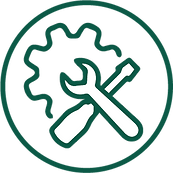
Prototyping
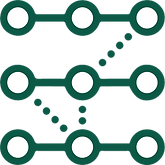
UX

Service Design

System Thinking

App Development
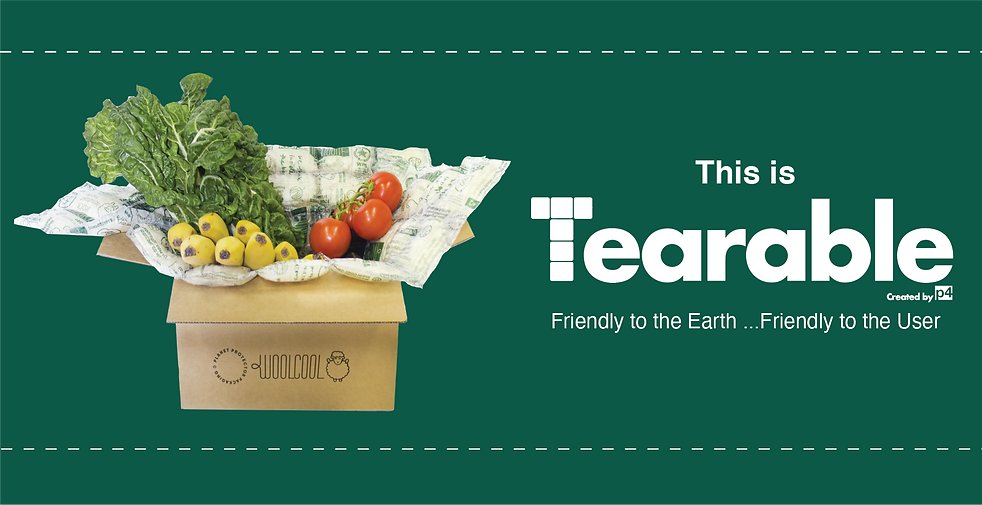
Designing Sustainable Packaging
The Overall Project:
This project was a group collaboration that lasted 13 weeks where our group was given the opportunity to work with a real-world client, to re-design their current packaging solution. The final design solution was successfully chosen to be further pursued by the client, where it is currently being patent. Where the client (Planet Protector Packaging) can produce it for real-world use. I really enjoyed the research and development side of the project, being able to find a problem in the current product, in order to improve their business values.

What is Tearable?
'Tearable' aims to improve the current cold food packaging service, to provide an internal box liner that is cost-effective, improves the user experience, and easy to manufacture, while also keeping the core values of the client's business model. The design utilizes waste wool and recycled plastic liners, where it'll be assembled into pouches using thermal seals and perforations. This allows for the user to tear the roll of the liner to any size they need depending on the carton the user is supplied with.
'Tearable' Features:

Pouch Liner
Tearable Design
Recycling Service
Recycled Wool
Cost-Effective
Sustainable
How It's Used:

Tape the bottom of the carton, leave the top open
With the sizing guidelines provided, tear roll to the specified size
Tear liner into the shape of your carton uses (as per guidelines)
Add cooling packs to the bottom of the carton
Add-in contents
Add-in additional cooling packs on top of the food
Tape top of the carton, ready for delivery
Educating The User:
The graphics on the liners are per pouch showing both your awards and information. A QR code links to education and information of how to recycle and reuse the product to ensure it does not reach a landfill end of life. Shows the user how to domestically recycle the liner or how to return back to the distributor.


Cradle to Cradle Sustainability:
Images of what machines will be used in the end of life, cost of implementation, the process mapped out (more in-depth than supply chain) Also show that the machines are scalable as well, so in the long term they can move onto better versions of the machines. Utilizing redcycle and replas (what they use currently) to recycle the plastic, and the wool can be repurposed back into the chain to be re-used accordingly, to save it from going to landfill.

Recycled wool and liners are collected and shredded
Wool and plastic spun to separate
Wool Sterilised
Materials processed into liners
Liners Vacuum packed and palletised
Roll sent to food distributor
Distributor lines boxes of food
Arrives at end-user and then recycled
The Design Process
The Problem:
From user study and interviews, it was found that many pain points were discovered in the supply chain of the liner. By improving these pain points can streamline the supply chain and ease of use. These pain points are marked as X, which can be further improved through research and development.

The Research:
In finding a problem with the client's current product, I used user experiences maps and value propositions to determine weaknesses that the user can experience. During user site visits, the user mentioned that the assembly of the packaging boxes can be confusing and slow, as the client offers 12 different sizes of packaging liner for the user to use. This is where I found a design solution of the user being able to tear to the size they want.
x
x

The Development:
In developing the idea further, I sketched out the idea with the concept of creating a design that allows for more streamlined construction for the end-user. The photo below illustrates the process of how the pouches can be constructed.
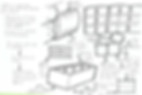
The Prototyping:
From the client meeting, they allowed us to further pursue this, which led to me making the right size pouch that can be able to fit all 12 cartons that the client supplies. While creating a sheet that can be torn to many sizes to fit each carton, where leftover pouches are a minimum, to lessen waste. This led to many prototypes which included the one below, where it showcases the design of the pouches, where perforations will surround the pouches.


Prototyping Tearing Feature
Prototyping Filling the Wool into Pouches
The Final Design:
The final design of the tearing packaging liner aimed to encompass all the values and beliefs of the client business. This is in regard to being cost-effective, have an efficient end of life cycle, be able to utilize the current materials that the client offers, easy to learn for the end-user, and be sustainable for future commercial uses.

Presentation to Industry Partner
What I Learnt:
I was really passionate about this project through how it solely relied on research and development for the design to succeed, from rapid prototyping to proposing new ways of integrating this idea into other industries. Learnt new ways in proposing new ideas to industry clients, and using the KISS (Keep it simple stupid) formula through the design process.
bottom of page