top of page
Similar Project:
This is another project that I led while at Evolve Group which is the Bin Bypass. A small-capacity donation station that aims to reduce bin diving and promote recycling initiatives throughout the community.
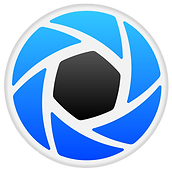
Keyshot Rendering/Animation
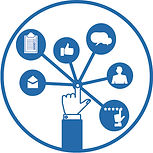
End to End Project Management

BOM, Part, Freight Optimisation & Costings
Skills in this Project:

Solidworks
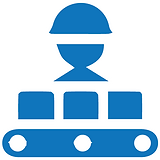
Plastic Injection Moulding

Photoshop/Illustrator
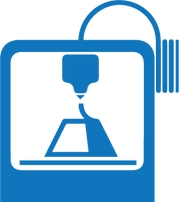
Rapid Prototyping

DFM & DFA Optimisation

Optimising For Manufacture & Assembly
The Overall Project:
This was a project that I led at Evolve Group, where our client came to us with an idea that they wanted to bring to reality. They gave us creative freedom to come up with a concept for them to review before proceeding further. The design had to be similar in size/capacity to a product that was being rolled out in WA. The aim for the client was to have the parts ready to be tooled, ease of assembly, and optimise material selection and design features for the context of use.
Please see link to Containers for Change Website for additional information:
https://www.containersforchange.com.au/qld/council-solutions

What is it?
The CoEx Pay it Forward Basket is a large capacity 10c bottle/can refund station where the general public can deposit unwanted cans/bottles for someone else to take and claim. This product aims to reduce the amount of bin diving and littering that currently occurring in Australia. This large-capacity product can be installed in high foot traffic areas where a lot of bottles/cans are deposited. This product is being rolled out in connection with Bin Bypass which a developing a small capacity station.
The Design:
The Pay it Forward was designed to be optimised for injection moulding. A 2 part design was chosen due to ease of assembly during installation, where the top piece would combine into a hinge located on the base part. This hinge would hold the lid in place and require a certain angle in order to be removed. Making it difficult to remove.
The material used is a locally sourced HDPE/PP blend resin that can be durable as well as withstands UV.

The Initial Prototypes:
During the design process, many 3D-printed prototypes were completed in order to perfect the snap fits, internal ribbing and how the cans/bottles would perform when deposited. This was crucial in creating a successful solution for the client before proceeding into tool manufacture.
The Technical Drawings:
Below is a sample of the technical drawings provided to the client to sign off the design to proceed with the final prototype. Once the prototype is signed off, we would proceed to quote for tool manufacturing.
What I Learnt:
This was one of the first projects that I worked on at Evolve Group, and it was a very eye-opening experience in designing products for plastic injection moulding. I learned a lot about the features of Solidworks and how to CAD models effectively for injection moulding. With regard to ribs, snap hooks, hinges, and material shrinkage specifications. I also learnt about pallet optimisation in creating a product that can be effectively packed onto pallets through carton stacking. At the time of writing, this project was heading into user testing the 1:1 prototype before moving into tool manufacture.

Bottle/Can Assembly:
The large capacity design allows user to easily deposit their cans/bottles like they're throwing them into a bin. When the lid is closed user deposit through the middle cut-out as if they're using a recycling bin.
Branding & Drainage:
Bottle/Can perforations are on the sides and front of the basket to allow for drainage but also adds subtle branding. Branding locations were on the upper sides and front, but also on the lid, giving the client flexibility as to what type of label they wish to apply.
Circular slots at the bottom of the product allow for water or liquids to drain through the product instead of building up and adding additional weight.


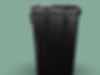
Rear Mounting:
The client aimed to have this product installed in numerous locations. Keyholes were utilised at the rear allowing the product to be installed on either poles or bins.
Other Images of the Pay it Forward:
The Overall Project:
This was a project that I led at Evolve Group, where our client came to us with an idea that they wanted to bring to reality. They gave us creative freedom to come up with a concept for them to review before proceeding further. The design had to be similar in size/capacity to a product that was being rolled out in WA. The aim for the client was to have the parts ready to be tooled, ease of assembly, and optimise material selection and design features for the context of use.
Please see link to Containers for Change Website for their story:
https://www.containersforchange.com.au/qld/council-solutions
The Concept:
Below is a sample of the concept phase the design went through, where a form study was conducted for the client on what shape they desire. Ranging from simple to complex forms, which gives the form a deeper character.
The Research:
Once we started the design phase, research was conducted into similar products that are currently in the market, and found there are limited amounts of plastic deposit bins, where metal enclosures are used instead. The below wire container is the size that our concept was based on as the client wanted a similar capacity.
The 1:1 Prototype:
When the detail design was finalised the client moved onto a 1:1 scale prototype made out of a black Polypropylene which represent similar to what the product would be inaction moulded from. This prototype is crucial for user/client testing as it is one of the last chances for finding any errors and flaws int eh design before moving to tool manufacture. As it would be costly and timely to make tool modifications to fix any design errors. I am proud to how this prototype turned out in the perforation details and the rear lid clip detail that allows the bucket lid to be easily installed and rotate without removing.

bottom of page